Özek Makina
has served for more than 90 plants across 20 countries since 1968.
Please visit www.rotarykiln.net for further information about our company, services and references.
Hot Kiln Alignment
& Roller Skewing
In Situ Tyre, Roller
Th. Roller Machining & Grinding.
Easy Bar
Tyre Bore Lubricant
Carbon Graphite Blocks
for Roller Lubrication and Seals
Hot Kiln Alignment
& Roller Skewing
We measure the actual kiln axis, slope of kiln and individual elements, shell deformation, ovality, tyre and roller diameters and roller skew precisely with latest technology, analyse all the data by the help of specific software and present in a detailed, clear and understandable report.
The easiest way of extending the kiln’s efficiency and life is to understand the current conditions.
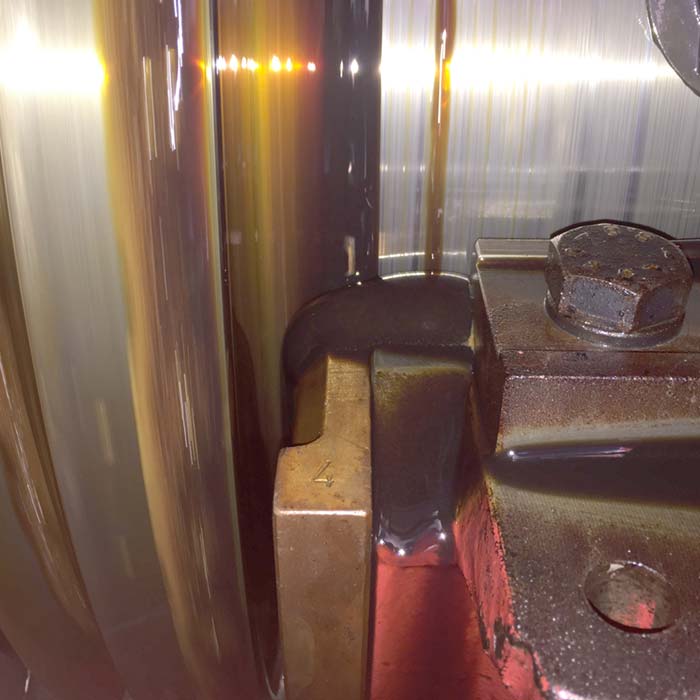
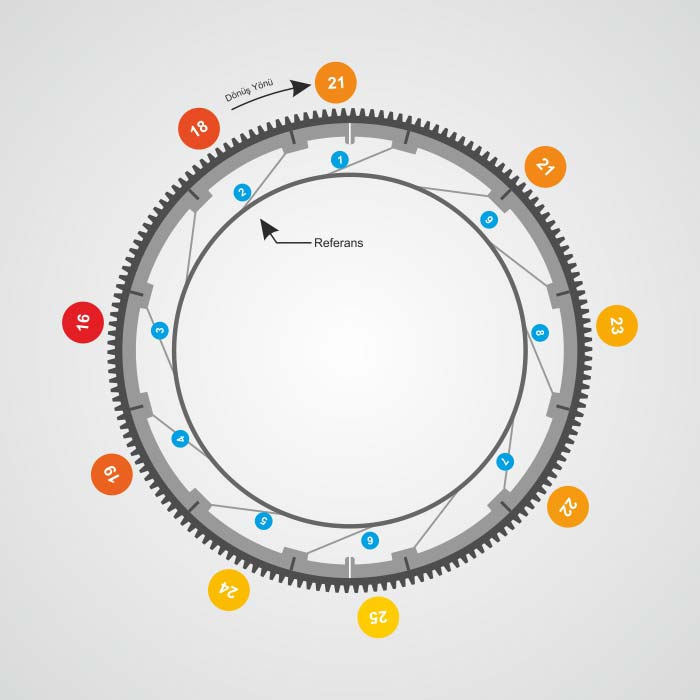
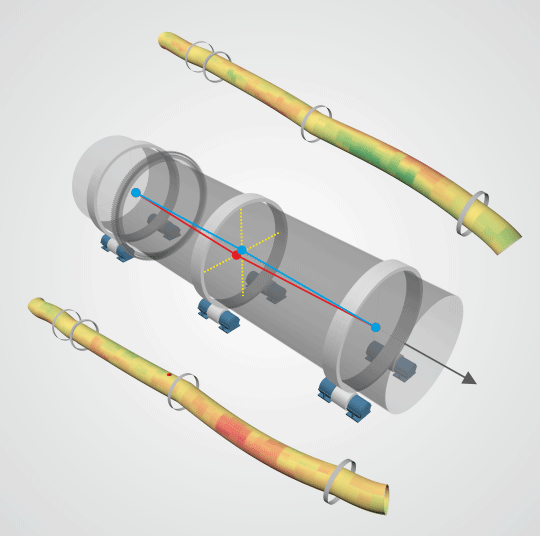


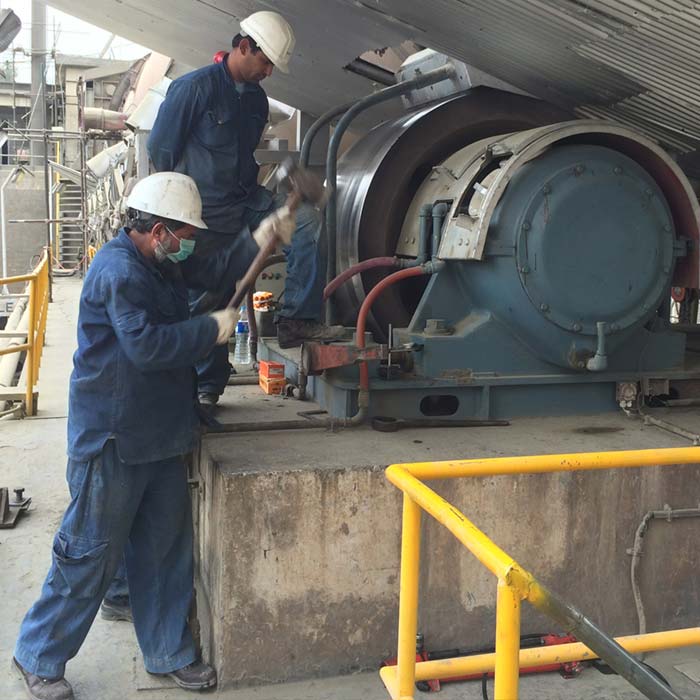
Analyse All Details
Inspecting a rotary kiln requires more knowledge and experience than standart survey services. We can determine and fix the problems by surveying the kiln with latest technology precise equipments, professional data analysis and our experience about kiln behaviours. Please study our sample report for more information.
Kiln Axis
We achieve the actual kiln axis generated by the roller and shell positions, gain the slope of kiln and individual components such as rollers, tyres, pinion and girth gear. Analyse the deviations and find out the necessary action to perfectly align the kiln back. These precise surveys are analysed with 50 years of experience combined with high engineering skills.
Shell Inspection
We scan the shell section by section to gain the deformation data of its plastic (such as collapses, cranks and eccentricity) and elastic (such as ovality) behaviours. We aim to extend the shell and brick life by complex analysis of shell, shell/tyre relations and kiln axis while proving the load distribution and pinion/girth gear relations.
Tyre & Roller Inspection
The axial migration of a rotary kiln is mostly related to its tyre/roller relations. Detailed analysis of informations such as the surface conditions and wear level of both tyres and rollers, bearings, lubrication efficiency, operating angels give us a high resolution photo of the current condition which helps us to suggest more realistic alignment actions.
Clean Report
After collecting the kiln data, we prepare and share our raw report while we are on site. We schedule a meeting with all relevant engineers to present our findings in a clean and understandable report supported with high quality graphics, charts, photos, videos and animations. It is the best time to discuss in depth about ongoing problems, our solutions and share some influential kiln maintenance knowledge.
Roller Skewing
After presenting our report and agreeing in solutions, we provide supervision services for alignment including roller skewing and bearing replacement if requested. We can extend our supervision services for shell, tyre, chairpad and girth gear reversal or replacement as a third party inspector with survey services or direct supervisor as a sub-contractor depending on the request.
Periodical Services
We believe that the best solution is to determine the problem before it stops you. We provide periodical site visits and kiln services including basic inspection for tyres, rollers, bearings, thrust roller, shell and seals, basic surveys and alignment supervision every 3-6-12 months depending on your request. Please contact us for more information about our periodical services that fits you best. >>>
On Site Machining & Grinding Services
for Tyre, Roller and Thrust Roller at up to 3,5 rpm
Ozek Makina provides on site machining and grinding services for tyres, rollers and thrust rollers of rotary kilns, rotary coolers and dryers, granulators and agglomerators in cement, gypsum, fertilizer, feed and petrochemical industries. We machine and grind the tyres and rollers at the same time and can work at up to 3,5 rpm for rotary kiln tyres and up to 5,0 rpm at rollers. We can clean out deepest pitting, conical, concave, convex or wavy wear profiles by our patented mobile machining and grinding technology.
Service at 3,5 rpm
We can resurface your tyres and rollers in normal operating conditions. There is no need to stop the kiln or even no need to slow down in some cases.
Machining & Grinding
Thanks to our patented mobile machining and grinding technology we can solve surface problems of tyres, rollers and thrust rollers in any level.
Following the Diameter
We measure and report the diameter and local deformation before, during and after our resurfacing services to decide next necessary actions.
Alignment After Resurfacing
We skew the rollers to tolerate the machined new diameter if necessary and provide hot kiln alignment and on site resurfacing services together.
Experience
Ozek Makina has provided more than 350 individual services at 90 plants across 20 countries since 1968 and gained a remarkable rotary kiln service experience.
Self-Devotion
We are on site with our team who can judge the problem from different perspectives, lucubrate with higher effort to perfect the solution and work parallel to the planned revision schedule.
On Site On Time
Our main goal is to help you to keep the kiln rotating hassle free. We focus on arriving at the plant with our tools in days time. Our engineering and logistics team is ready for any international call.
World Wide Service
After servicing almost all Turkish plants, we have proudly serviced for more than 90 plants across 20 countries in a wide geography from America to Vietnam. We guarantee %100 customer satisfaction.
Ozek Makina is providing the American one-of-a-kind Easy Bar® tyre bore lubricants to EMEA countries.
Easy Bar® is a solid high-temp lubricant bar that melts when placed on the hot surface of a kiln or dryer shell. Easy Bar®’s patented blend of graphite, mineral and metal lubricants are suspended in a solid polymer binder. When placed between the tire and the kiln shell, the carrying agent melts and releases the lubricants. The rotation of the kiln distributes the lubricants over the filler bars and inside the tire bore.
Easy Bar® melts at 49°C with an auto-ignition point of 538°C. The only kiln lubricant bar that will NOT AUTO-IGNITE during application.
100% Lubricant
~ 40% Graphite
~ 10% Copper
~ 50% Binder
* Contains no chlorine, bromine or other halogens that create health risks.
538°C Auto Ignition Point
Melting Point: 50°C
Auto-Ignition Point: 538°C
This ensures worker safety and no dangerous flame-ups.
Homogeneous Lubrication
When placed between the tire and the kiln shell, the carrying agent melts and releases the lubricants. The rotation of the kiln distributes the lubricants over the filler bars and inside the tire bore.
Practical & Efficient
Easy Bar® shortens and eases the tyre bore lubrication process. Homogeneous lubrication is no longer based on crew’s ability. All is placing the bar between tyre and shell.
EASY BAR® employs principles of lubricity and physics to assure proper lubrication of kiln and dryer tires. First, it contains high quality, non-petroleum, synthetic lubricants. It also contains a fine metal powder that exploits the lubricating benefit of dissimilar metals.
Once melted, uses the motion of the kiln to distribute its lubricants to the mating surfaces of the tire bore and kiln shell. As the lubricants are distributed by the motion of the kiln, a thin, temperature resistant film forms a lubricating barrier between the moving surfaces, as well as fills the microscopic imperfections that are typical on metal surfaces.
- Lubricate all tyre bore homogeneous
- Reduce kiln lubrication time and effort
- Maintain creep
- Protect the shell during start-ups and shutdowns
- Increase Wear Pad Life +50%
- Minimize / Eliminate Weld fractures
- Extend Refractory Life
- Minimize Shell Ovality
The Right Solution for Tyre/Roller/Th. Roller Lubrication
Carbon Graphite Blocks in Requested Sizes
Carbon graphite blocks which are specially produced for rotary kiln tyre, roller, thrust roller and seals can continue efficient lubrication even under extreme loads thanks to its layered chemical structure and direct contact installation. Our carbon graphite blocks are designed for rotary kilns based on kiln rotation speed, surface hardness of tyre and rollers and lubrication needs. They provide homogeneous and efficient lubrication thanks to their direct contact installation. All our products are shipped worldwide right after the order, in your requested sizes.
Special for Rotary Kilns
Best Quality Material
Efficient Lubrication
Hi-Resistance